When you buy climbing ropes online, have you ever noticed the “22kN tensile strength” label on the package? This seemingly simple number has reduced rock climbing accidents in Yosemite National Park by 47%. Today, we will discuss the key mechanical index of tensile strength.
What is tensile strength?
Tensile Strength Reality Revealed
During the 2018 collapse of the Morandi Bridge in Genoa, Italy, engineers discovered the key cause in the wreckage: a 38% drop in the tensile strength of the rusted steel cables. It was this 38% drop that made the steel cables no longer able to withstand the high loads that led to the accident.
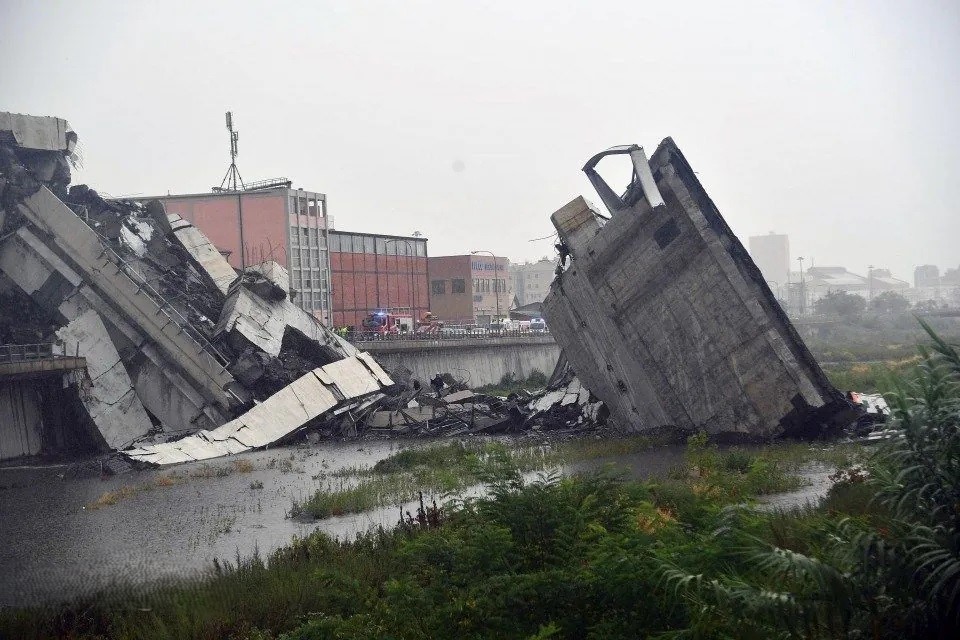
Define
Tensile strength is the maximum stress that a material can withstand before it is pulled apart in a tensile test, and the unit is usually: MPa. The formula: σ=F/A may seem simple, but it will give us a lot of insight.
Assuming a 6mm diameter 304 stainless steel bar, the force required to pull it off is equivalent to lifting three family cars at the same time (about 530MPa). However, in practice, engineers will allow at least 1.5 times the safety factor.
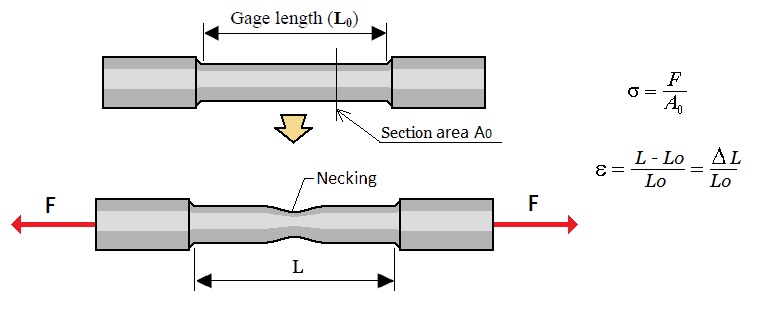
Tensile Strength vs Yield Strength
Many people will confuse tensile strength with yield strength. Let’s take a tension spring as an example, yield strength is the scale at which the spring begins to permanently deform and cannot spring back, while tensile strength is the last frame before the spring is completely pulled apart. In the Boeing 787’s aluminum frame design, the difference between these two values determines how many turbulent impacts the aircraft can withstand.
How to measure tensile strength?
Want to know the tensile strength of a material, the most common method is to use the universal testing machine: first of all, the material should be processed into a standard “dumbbell” shaped specimen, clamped at both ends and then stretched at a constant speed, the machine synchronized recording of tensile force and deformation data.
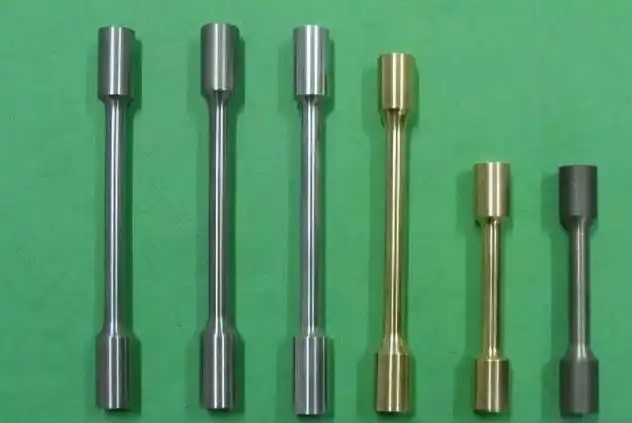
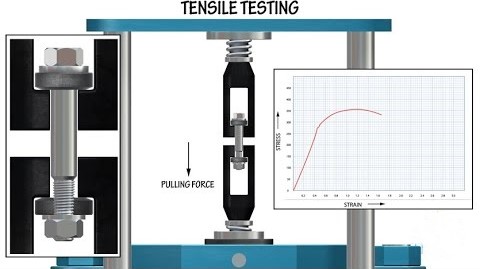
A quality inspector at an automotive plant found a 12% difference in test results between the same batch of steel in a hydraulic fixture and a mechanical fixture. This is because the biting force of the fixture changes the stress distribution of the specimen, so we have to follow the ISO 6892-1 standard for testing.
But then, testing standards vary from industry to industry:
- ASTM E8 (U.S.A.): Specimen dimensions are accurate to the millimeter scale and require constant laboratory temperature.
- ISO 6892 (International): more focused on strain rate control, suitable for high precision studies.
Frequently Asked Questions and Solutions
Problem 1: Large fluctuations in test results?
→ Check whether the specimen is clamped off-center or whether there are scratches on the surface.
Problem 2: Data deviates from literature values by more than 5%?
→ Calibrate the sensors and confirm that the laboratory temperature and humidity are in compliance.
It is recommended that newcomers use 6061 aluminum alloy (tensile strength of 290MPa ± 10) as a “control sample” to verify the reliability of the test procedure.
Stress-Strain Curve
When the universal testing machine test is finished, the system will automatically generate the stress-strain curve. If the material is compared to an athlete, the stress-strain curve is its physical fitness test report. The curve of mild steel is like a steady mountain climber, while cast iron is like a sprinter who suddenly loses strength. The coordinate value of the highest point of the curve is the tensile strength of these materials.
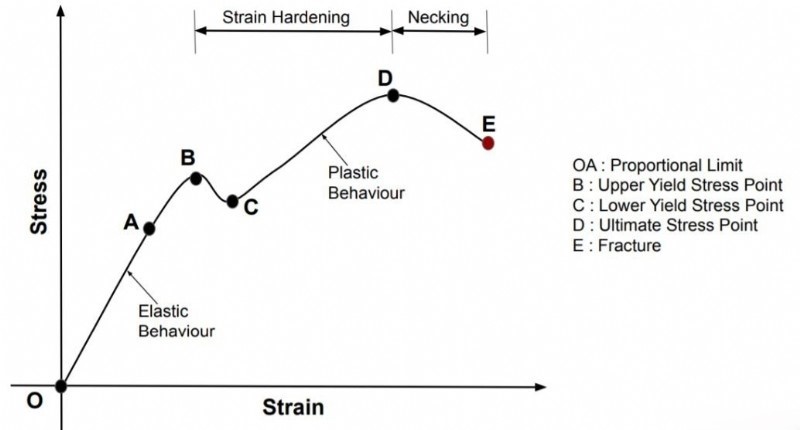
What Factors Affect Tensile Strength?
First of all, the type of material is the core factor: steel has a tensile strength of up to 1,500 MPa, which is 30 times stronger than ordinary plastic (50 MPa). Carbon fiber composites are even stronger than steel through the directional arrangement of fibers, but this tensile strength will only be reflected in one direction.
Environmental factors should not be ignored: steel becomes brittle at low temperatures, and tensile strength can plummet by as much as 20%. Humidity can also “compromise” the strength of some materials (e.g., nylon softens when it absorbs water).
At the microscopic level, the smaller the grain size inside the material (refined by heat treatment), the fewer the impurities and defects and the higher the tensile strength. This is why aerospace alloys are melted repeatedly to remove air bubbles.
How can I Increase the Tensile Strength of My Materials?
Here’s a guide to take you through 3 common ways to strengthen metal materials:
- Alloying: In the process of refining, adding some metals in proportion can change its physical and chemical properties, such as adding carbon to iron to make steel, which is five times stronger than pure iron.
- Cold working: Repeated rolling of the metal to produce a hardening effect.
- Heat treatment: e.g. the use of quenching to form a high hardness martensite inside the steel.
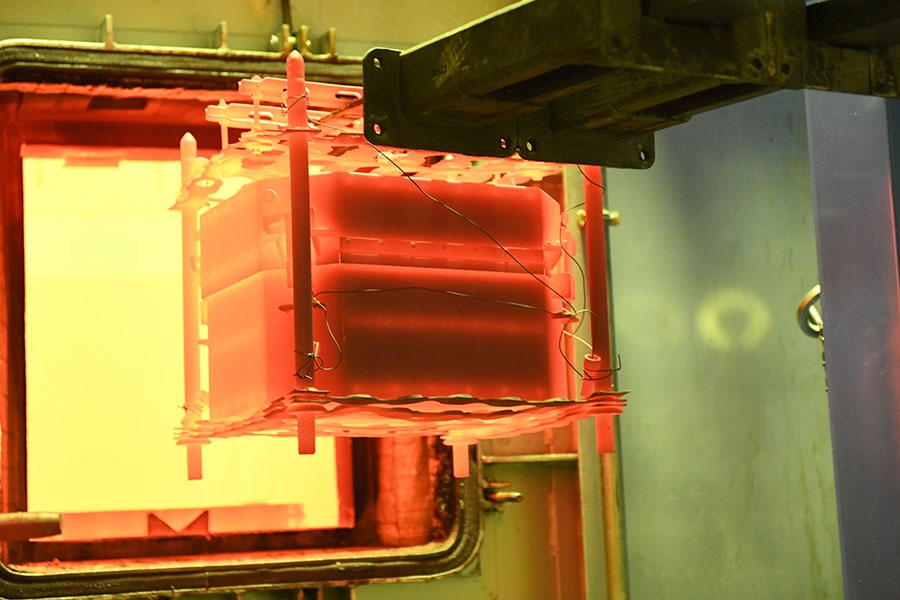
There are also emerging technologies, such as 3D printing, which customizes microstructures by melting metal powders layer by layer with a laser.NASA previously developed a GRX-810 superalloy, which has two times higher tensile strength than conventional nickel-based alloys, and has been used in rocket engines.
Common Myths and Truths about Tensile Strength
Myth 1: “The higher the tensile strength, the better.”
Truth: Super-strong materials can come at the expense of toughness. For example, ceramic knives are extremely hard, but break easily when dropped on the ground.
Myth 2: “Laboratory data equals actual performance”.
Truth: The effective strength of a bolt may decrease by up to 40% under prolonged vibration and corrosive environments.
Myth #3: “Materials with high tensile strength never break.”
Truth: Tensile strength only represents the limit value of one-time pulling off, but in reality the material is more because of “fatigue” and breakage. 2015 German high-speed rail wheel breakage accident, wheel steel tensile strength up to the standard (1,200MPa), but because of tiny cracks for a long time accumulation (fatigue strength is not enough), and ultimately collapsed at high speeds. The wheel steel had the standard tensile strength (1200MPa), but because of the long-term accumulation of tiny cracks (fatigue strength is insufficient), it finally collapsed at high speed. Therefore, high tensile strength ≠ durability, under dynamic loads need to pay extra attention to fatigue life.
Myth 4: “The values on the test report can be used directly”
Truth: Laboratory data is ideal, but differences in real-world environments can diminish material performance, such as extreme weather and corrosive environments.
Common Sense for Engineers
Relationship between tensile strength and other mechanical properties
Fatigue strength is another key indicator: aircraft wings can break due to metal fatigue even when subjected to dynamic loads well below the tensile strength. Therefore, a comprehensive assessment of a material’s “versatility” is required when selecting a material.
Economy Balance Program
HRB400 rebar, commonly used in construction sites, is $200 per ton more expensive than HRB335, but has a 20% higher tensile strength. Engineers found that by using the former in buildings with more than 30 floors, the overall steel usage is reduced by 15%, and the overall cost is instead reduced by 8%.
Summarize
When you see here, I believe you have a certain understanding of the tensile strength of the material, but this is only some theoretical knowledge and some cases, if you want to go further to understand the tensile strength, can only rely on your future practice and experience.
EVERGREEN Machinery is a manufacturing plant that integrates casting, forging, CNC and sheet metal working, we have perfect manufacturing process and quality control. The production equipment is also very complete, if you happen to be looking for a supplier, you may want to know about us.