What is an Iron-Carbon Phase Diagram?
Iron-carbon phase diagrams are mainly used to study iron-carbon alloys, which will graphically show the different morphological characteristics of iron-carbon alloys under different temperatures, pressures or other chemical conditions.
You can understand that a person will show different states under different environments and moods, and the Iron-Carbon Phase Diagram is equivalent to a photo will record this state, and then you can analyze the person based on the photo (Iron-Carbon Phase Diagram) and come to the conclusion that you want.
How to Read Iron-Carbon Phase Diagrams
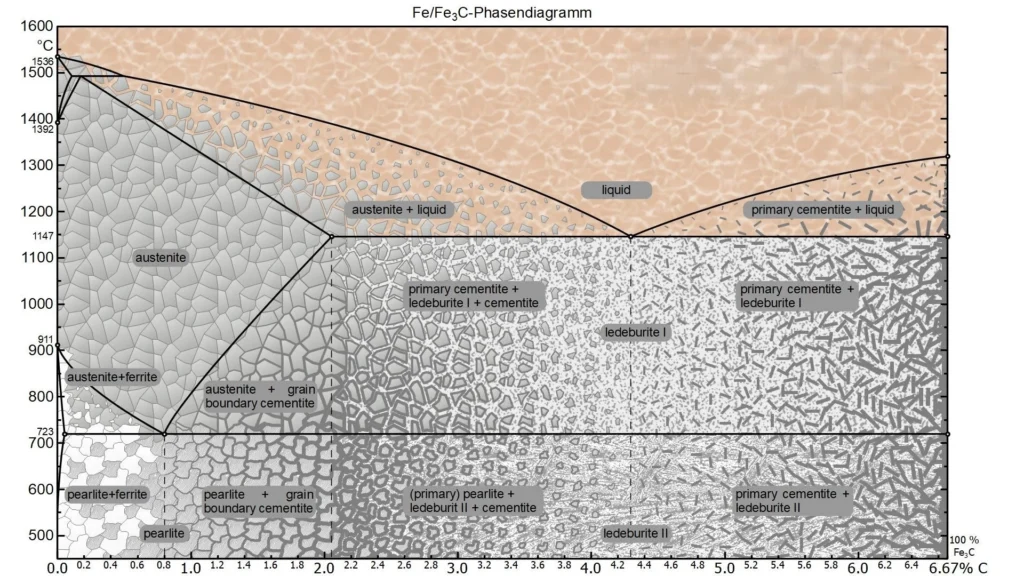
You can observe the picture above, this is the iron and carbon phase diagram, the vertical axis (Y axis) represents the temperature, and the horizontal axis (X axis) represents the carbon content in the iron. There are some special temperatures and they are labeled for you, for example, the node at 723°C represents the critical temperature for the transformation of the austenite phase of iron to the pearlite phase, and 1147°C represents the formation of austenite if the steel is heated further.
The number on the horizontal axis represents the carbon content, carbon content of 0.0218% to 2.11% between, is what we often call steel, while the carbon content of more than 2.11% is known as cast iron, and steel, both steel and cast iron, they are a mixture of iron and carbon, but only the proportion of carbon is different.
Another conclusion is that the higher the carbon content (but not greater than 6.67%), the harder and more brittle the metal exhibits its properties, and conversely the lower the carbon content, the softer and tougher it behaves.
Iron-Carbon Phase Diagram
Next we look at some important nodes as well as demarcation lines on the iron-carbon phase diagram together in detail, which can provide you with some substantial help for future manufacturing and research.
Types of Ferrous Alloys on The Phase Diagram
There are a total of seven alloy types on the iron-carbon phase diagram, and the main way to distinguish between these seven is by the carbon content and the reactions that have taken place.
Industrial Pure Iron
The carbon content of industrial pure iron is less than 0.0218%, it shows the organization at room temperature: ferrite (F) + tertiary carburite (Fe3C Ⅲ), the following is its metallographic diagram.
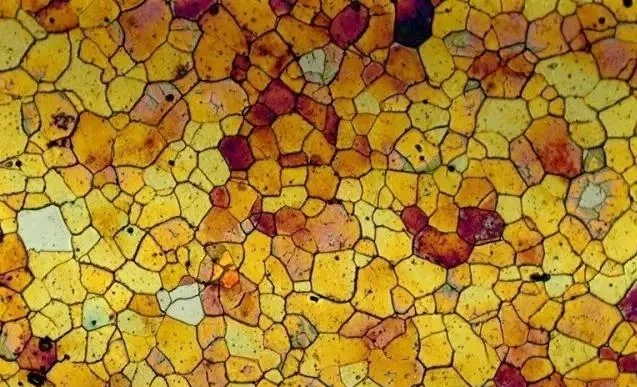
The texture of industrial pure iron is particularly soft, toughness and electromagnetic properties are also particularly good, usually will be used as deep-drawn materials, stamping into some of the requirements of the strength of the complex shape; or as electromagnetic materials. Of course more are used for smelting alloys.
Hypereutectoid Steel
The carbon content of sub-eutectic steel is between 0.0218% and 0.77%, and its crystallization reaction process is: homogeneous crystal reaction+ inclusion crystal reaction + solid solution transformation reaction + eutectic reaction. Under normal conditions, its internal organization consists of pre-precipitated ferrite (F) + pearlite (P), and the amount of pearlite increases with the increase of carbon content.
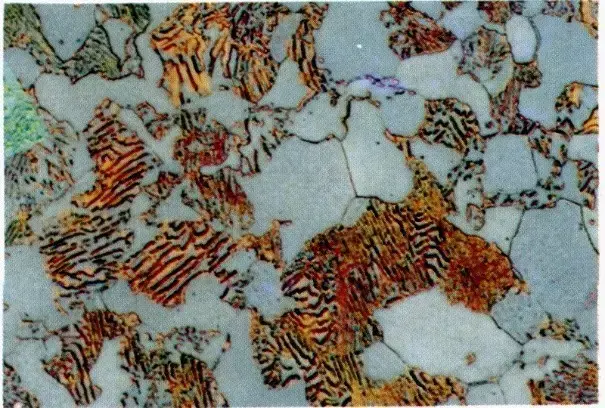
Our common Q235 steel belongs to the category of sub-eutectic steel, the toughness, weldability and plasticity of this type of steel are very good, suitable for some welded structures.
Eutectic Steel
Eutectic steel has a carbon content of 0.77, and after homogenization and eutectic reactions, the internal organization is 100% pearlite (P), with a relative weight ratio of ferrite and carburite phases of 8:1.
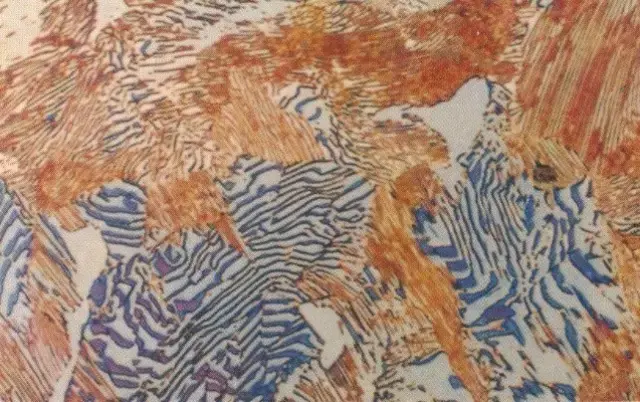
Eutectic steels are better suited for higher strength components such as bearings, gears and cutting tools.
Hypereutectoid Steel
Hypereutectoid steel has a carbon content between 0.77% and 2.11%, the reaction of the crystallization process is: homogeneous reaction + secondary precipitation reaction + eutectoid reaction, its internal organization is pearlite (P) + secondary carburite (Fe3C II), Fe3C II will be along the austenite grain boundaries in a network precipitation, which will make the material overall brittle.
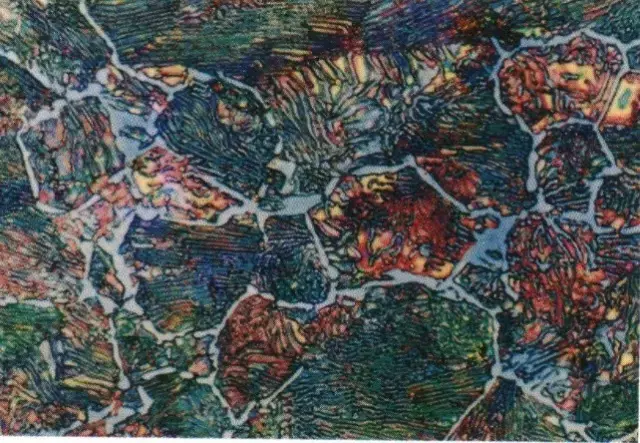
As the carbon content increases, it also means that iron-carbon alloys become harder, but also more brittle. The same is true for peritectic steel compared to eutectic steel, where you can change its internal organization and properties through heat treatment.
Eutectic White Cast Iron
Carbon content between 2.11%-4.3% is called sub-eutectic white cast iron, its crystallization process to undergo homogeneous crystallization reaction+ eutectic reaction + secondary precipitation reaction + eutectic reaction, the internal organization at room temperature is manifested as follows: pearlitic (P), secondary carburization (Fe3C Ⅱ), low-temperature Leydenite (Ld’).
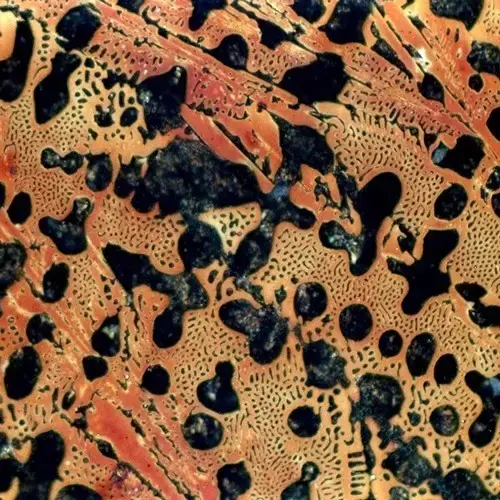
The more prominent advantage of sub-eutectic white cast iron is wear-resistant, you can use it to make some wear-resistant parts, or very good.
Eutectic White Cast Iron
Carbon content of 4.3% of the iron and carbon mixture known as eutectic white cast iron, it is the organization at room temperature only low-temperature Leistungite (Ld’), but his crystallization process is required to go through the eutectic reaction, secondary precipitation reaction and eutectic reaction.
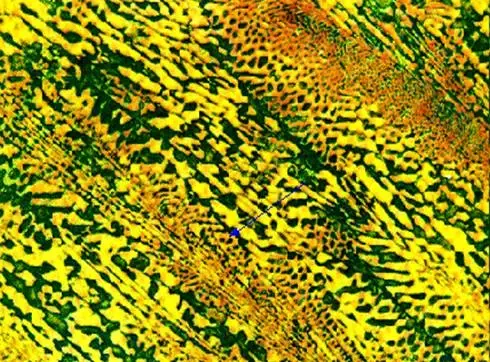
Eutectic white cast iron is extremely hard, but it has little plasticity and is prone to brittle fracture.
Eutectic White Cast Iron
Carbon content greater than 4.3% belongs to the over eutectic white cast iron, its crystallization process after the homogeneous crystal reaction, eutectic reaction, secondary precipitation reaction and eutectic reaction, room temperature organization: a carburite (Fe3C) + low temperature Leistungen (Ld’).
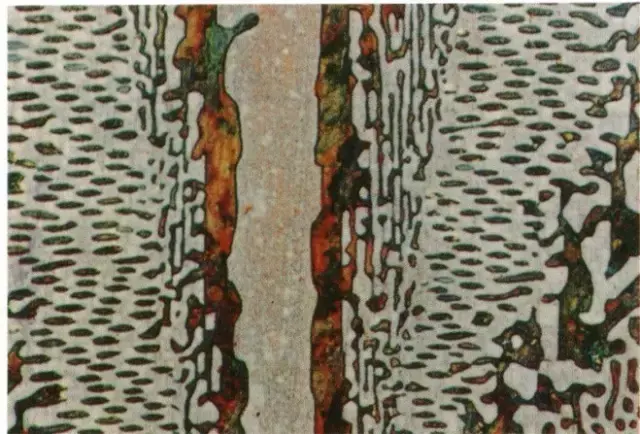
Compared to the other two types of white cast iron, per-eutectic white cast iron is the most brittle, but also the hardest, and you can use it to make some wear-resistant parts used in the mining industry, oil exploration, and other industries.
Boundaries
Boundary is also known as the critical point, which exists in the form of a line in the iron-carbon phase diagram, it is mainly expressed in the same temperature, different carbon content of the metal (or the same carbon content, different temperatures) to show the internal different proportions of the organization and after the reaction.
Eutectic and Eutectic Points
The so-called eutectic point, which you can understand as the point of co-crystallization, or point C on the iron-carbon phase diagram, refers to the point at which austenite and carburite precipitate out of the liquid at the same time and co-crystallize together to form leucite. A carbon content of 4.3% and a temperature of 1148°C are required.
The same is true for the eutectic point, which is the co-precipitated S-point, where α-iron and carburite precipitate from the austenitic phase to form a pearlitic organization.
Phase Fields
A phase field is a number of regions divided by a boundary, each of which contains one or two phases, and if there are two phases, then their proportions vary according to temperature and carbon content. If the boundary is reached, a phase change occurs.
Different Phases
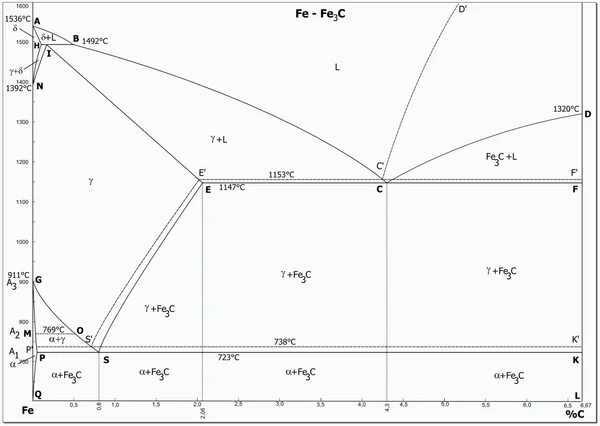
Ferrite
The organization and properties of ferrite are similar to those of industrial pure iron, with magnetic properties, good toughness but insufficient strength and hardness. It is stable up to 912°C, but transforms to austenite once it exceeds that temperature. As the carbon content increases, the ferrite decreases and is replaced by an increase in pearlite.
Austenitic
Austenite is a high-temperature phase, stable within 1148%C, hard and plastic, and is a good basic development of steel.
Carburization
The carbon content of the carburized body is particularly high, distributed in the rightmost side of the iron-carbon phase diagram, fixed all as high as 800HB, but the toughness is almost 0.
Pearlitic
Pearlite is a mechanical mixture consisting of ferrite and carburite, which has properties intermediate between those of ferrite and carburite. Depending on the temperature transition, pearlite can also be categorized as soothingite and flexuralite, although they are not fundamentally different.
Lycopene (Chemistry)
Rheinzite is a mechanical mixture of austenite and carburite crystallized from solution at 1480°C from a mixture of iron and carbon containing 4.3% carbon. However, since austenite transforms to pearlite at 727°C, it is composed of pearlite and carburite at room temperature.
Why is the Iron-Carbon Phase Diagram Important?
- It can help us utilize and develop iron-carbon alloys more efficiently for a variety of engineering and manufacturing needs.
- It is possible to understand the properties of alloys and predict phase transformations by means of iron-carbon phase diagrams, which are important guides for optimizing alloy compositions and heat treatment processes.
- The rate of heating and cooling can be precisely controlled according to your desired microstructure.
- Reduce trial and error costs by selecting the right process for machining different materials.
- We can guide factories to manufacture high-quality raw materials.
Summarize
Iron and carbon phase diagrams are a bit difficult for beginners to understand, you need to understand it, what each different position represents, what some key points represent. Don’t be discouraged, study it more and you’ll find it’s actually quite simple.
If you can master Iron-Carbon Phase Diagram and can apply it to real production, you will find that it is really great. It can help you realize innovation, improve quality and productivity.