CNC machine tools can be said to be in the metal processing industry is very common a kind of equipment, it has a lot of different types, almost all the metal processing process, cutting, milling, grinding, drilling, punching, engraving, bending, and so on some of the process.
Together with this article, we’ll take an in-depth look at what a CNC machine tool is, the different types it can be, what the benefits are, and of course some advice on purchasing equipment or choosing a supplier for your project.
What is a CNC machine?
CNC machine tools can be said to be the most common manufacturing equipment in the machinery manufacturing industry. Unlike traditional manual machine tools, CNC machine tools require engineers to write a program in the computer, and then the computer controls the machine tool through the written program, which allows it to automatically perform a variety of machining tasks.
CNC stands for Computer Numerical Control. You need to use the design software first, to design the part and the path of the tools and cutters that will be used in the machining process, and then use the programming system to write it as a code recognizable by the CNC so that it can follow the program to machine the part you want.
Dominance
Anyone involved in the production of industrial parts knows that precision, efficiency, safety, and cost savings are always in demand. Most companies start with manual machining, a process where dimensions can easily deviate, resulting in inconsistent products and requiring one person to operate a machine tool at an unmanageable cost.
CNC machine tools are the opposite, according to the same program to process out the parts are almost the same, stable quality, and precision and efficiency are very high, can be a person at the same time to control a number of equipment, greatly reducing the cost of labor. Improve the competitiveness of your business.
How do CNC machines work?
CNC machines work simply by following the program you have designed for them step by step, such as which tool to use at first, which tool to run from where to where, and then see if you need to run it again, and if not, next switch the tool and follow the path to machine the part.
The basic components of the CNC machine system
CNC machine tools are made up of many components that only work together to perform precise automated machining that would otherwise not be possible, and these components include:
Input Device
Input device refers to the piece of CAM that has written the program into the CNC machine tool equipment, it has many forms, such as a keyboard (can directly enter the command code), and a U disk (will have written the program into).
Machine Tool
A machine tool is a mechanical device that performs machining, which can be a lathe, a milling machine, a punch press, and so on.
The machine tool usually consists of a sliding table and a spindle, the table mainly controls the movement of the X- and Y-axes, and the spindle controls the movement of the Z-axis, and their main role is to control the position of the part and the speed of tool rotation.
Machine Control Unit (MCU)
The MCU is equivalent to the core part of the CNC machine, which is mainly responsible for receiving, analyzing, and executing the program you have written, thus controlling the movement of various parts of the CNC machine, such as the movement of various axes, switching on and off of the machine tool, changing tools and so on.
Servo Motors
If the MCU is the “brain” of the CNC machine, Servo Motors is its “heart”, which is responsible for receiving signals from the MCU and then driving the machine’s axes to make them move precisely along the X, Y, and Z, or some other additional axes.
It is responsible for receiving signals from the MCU and driving the machine’s axes to move precisely along X, Y, Z, or some other additional axis. To put it bluntly, it’s all about precise positioning and motion control.
Feedback Devices
Feedback devices are used in conjunction with servo motors, which provide real-time feedback to the MCU on-axis position information during axis movement, allowing the MCU to monitor and adjust the position of the machining axes during the machining process.
Tooling
Tooling is used in the machining process of some of the tools, such as some of the tools, drills, collets and shanks, etc., common CNC machine tools have a tool magazine to store a variety of tools, according to the process of automatic tool change.
Workholding Devices
Workholding devices are devices that hold the workpiece in place during the machining process. If they are not held in place, the workpiece will wobble or even damage the cutter head during machining. Common work-holding devices include clamps, chucks, fixtures, or homemade fixtures.
Operator Interface
Operator interface mainly consists of a screen and some buttons or a computer, mainly used to let the operator and the CNC interaction, the operator can write some simple programs or real-time monitoring of the machining situation.
Types of CNC machines
CNC machine tools have been around for more than 70 years, and after all these years, a wide variety of CNC machines with different functions have been developed.
CNC Milling Machine
The main function of a CNC milling machine is to get the product you want by cutting off the excess material from the workpiece. All you need to do is to give it a program and then press start after fixing the workpiece on it and it will be shaped precisely.
The tool magazine of a CNC milling machine can hold many tools, and each different tool is a different machining process. Commonly used tools are end mills (for milling), reamers (for reaming or repairing holes), face milling cutters (for milling flat surfaces), taps (for machining internal threads), and drills (for drilling).
CNC milling machine can be divided into vertical and horizontal, their main difference is the direction of the spindle, vertical milling machine spindle is vertical direction, while horizontal milling machine spindle is horizontal direction, so the horizontal milling machine can accommodate larger workpieces.
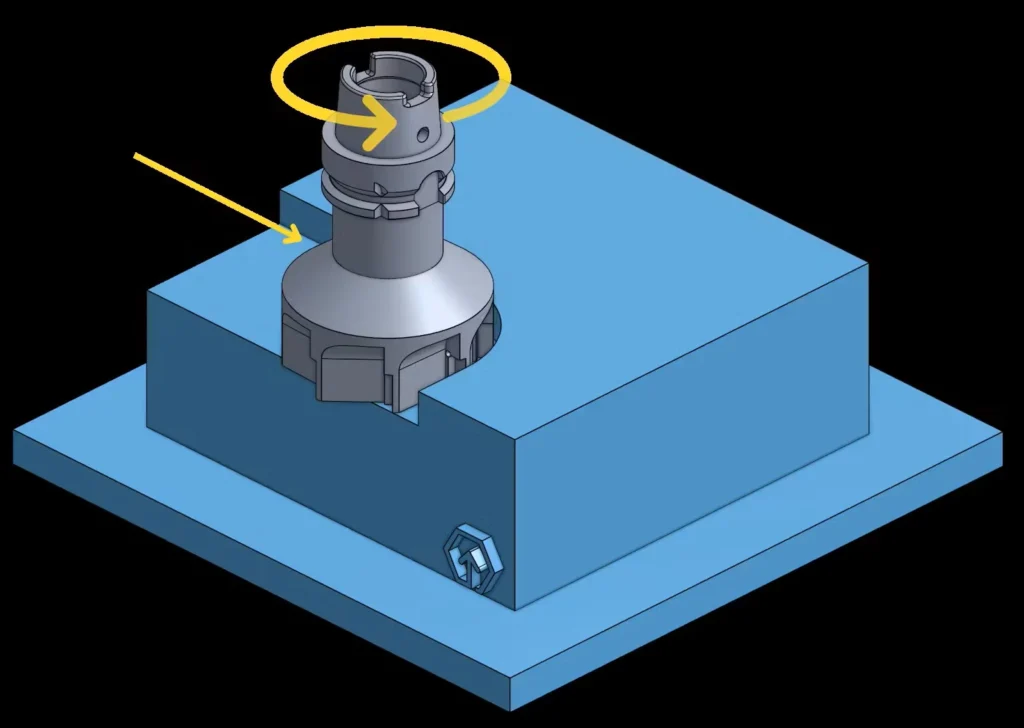
CNC Plasma-Cutting Machine
The main role of the CNC plasma cutting machine is used to cut sheet metal, it should be noted here, that plasma cutting can only cut conductive materials, non-conductive can not be cut.
The CNC plasma cutter will automatically cut the shape you want according to the program you have written, and you can also adjust the power when cutting according to the thickness of the material. He can cut thicker materials and cut very fast.
CNC Lathe Machine
The working principle of CNC lathe is to put the workpiece on the spindle, and then let the workpiece rotate with the spindle, and the tool can be moved back and forth and left and right to process the workpiece. The spindle is fixed and can not be moved, can only be rotated, so CNC lathes are basically processing some cylindrical workpiece.
The CNC lathe can also automatically change the tool head and can perform processes such as drilling, turning, knurling, finishing, and roughing.
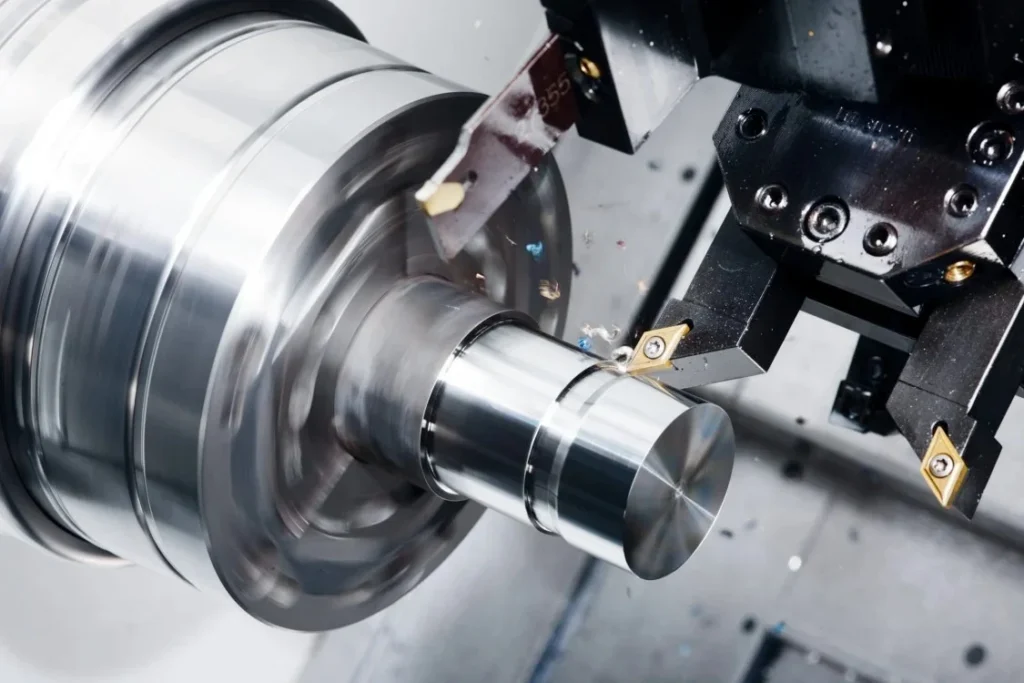
CNC Laser-Cutting Machine
A CNC laser cutting machine works similarly to a CNC plasma cutting machine, but works on a different principle; a laser cutting machine cuts material by using a high-energy laser beam.
If you use a laser cutter for cutting work, you will find that it cuts quickly, accurately, and with a narrow cutting width, which reduces waste.
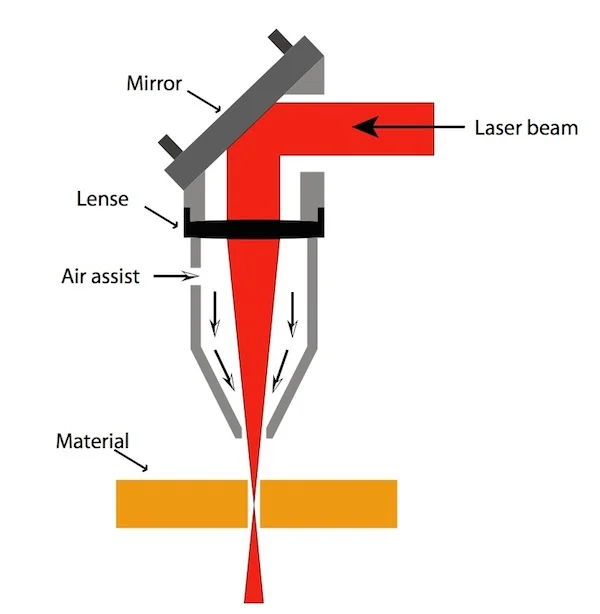
CNC Grinding Machine
The main purpose of using a CNC grinder is to grind and polish the workpiece, which is fixed on the machine, and then you have the option of grinding the workpiece using abrasives such as grinding wheels, sandpaper, or oil stones.
CNC grinding machines can realize high-precision machining in the nanometer scale, and with a high degree of automation, they are suitable for machining cylindrical workpieces, of course, plates are also possible.
CNC Drilling Machine
The main function of CNC drilling machine is to drill holes and holes in the workpiece. Of course, it can also use different drills to drill different holes, such as centering drills, deep hole drills, auger drills, and clamping reamers.
It’s a bit of a one-trick pony, but it’s still very useful to use.
CNC Water Jet Cutting Machine
The main function of CNC Water Jet Cutting Machine is to cut, it is to add the water stream to a very high pressure and then sprayed from the nozzle, of course there are materials that can’t be penetrated, then some fine abrasives will be added to the water, so that it can cut thicker metals.
During the cutting process, waterjet cutting generates limited heat, so there is no heat-affected zone, but the CNC Water Jet Cutting Machine has a big disadvantage in that the cutting speed is very slow, and the payroll efficiency is low.
Electric Discharge Machine
The processing principle of an Electric Discharge Machine is to process the material by using an electric spark discharge. The conductive workpiece is put into the working fluid, and each discharge will evaporate a thin layer of metal on the workpiece, and the processing speed is still very slow.
Electric Discharge Machine is very suitable for machining super hard materials which are difficult to be handled by traditional cutting methods, as well as parts with complex shapes, such as titanium alloy, tool steel, hard alloy, etc. It is suitable for die-casting molds, cavities, punching molds, etc.
Multi-Axis CNC Machine
A common CNC machine today is 3-axis, meaning it can move in 3 directions, while a multi-axis CNC machine represents 4 or more axes, which can move in 4 or more directions. This means that a multi-axis CNC machine can machine complex parts that cannot be machined in 2 or 3 axes.
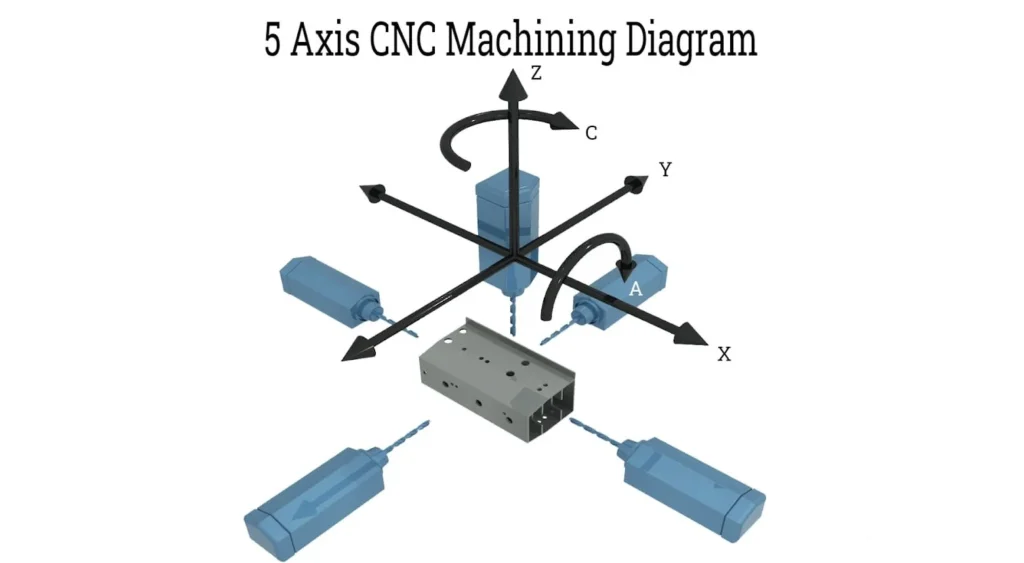
CNC Punch Machines
A CNC punch press is a sheet metal processing machine that uses a pre-prepared stamping die to punch and form the sheet. Like the cutter head, the stamping die can be changed automatically, you just need to prepare the program, put in the plate, and it can process it for you automatically.
CNC Tubing Bender
The main role of the CNC pipe bender is to bend the metal pipe into a variety of angles, you can avoid wanting to bend the pipe when the welding process, reduce manual intervention, but also to save costs.
Bender can be roughly divided into three categories, namely, roller bender (the use of multiple rollers to bend the pipe), stamping bender (the use of punches and molds to bend the pipe), stretching bender (by stretching the pipe to achieve bending).
3D Printer
3D printing machine can be said to be very flexible and versatile material molding equipment, why it is said to be versatile, this is because it is suitable for many different materials molding. However, it is not very efficient.
Types of CNC machine tools by number of axes
Above we are classified according to the different types of CNC machine tools, of course, we can also be divided according to the number of axes.
2-Axis CNC Machines
The minimum number of axes in a CNC machine is 2, if it is less than 2 then the machining task cannot be accomplished. These two axes are composed of the X-axis, which is responsible for horizontal movement, and the Z-axis, which is responsible for vertical movement.
2-axis CNC lathe can only do some relatively simple work, such as turning, milling drilling, etc., and can not be capable of some difficult processing tasks.
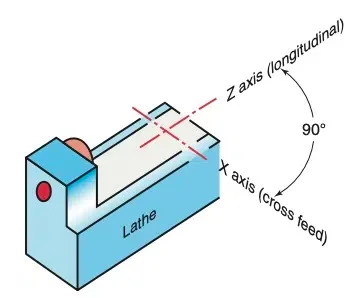
3-Axis CNC Machines
The 3-axis CNC machine tool is our most common, it in the two-axis X and Z axis on the basis of a Y axis, the three axes are perpendicular to each other to move, and the two-axis is more suitable for processing some of the more complex parts.
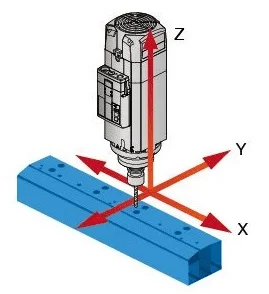
4-Axis CNC Machines
Four-axis CNC machines add an A-axis to the X, Y, and Z axes. This A-axis can be rotated on the X-axis, which allows the machine to machine on multiple faces of the workpiece, providing more machining flexibility for four-axis CNC machines. And there is no need to remove the workpiece for re-clamping.
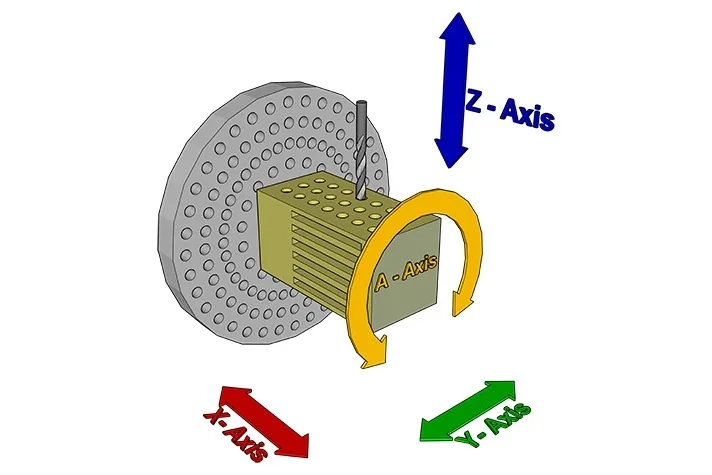
5-Axis CNC Machines
The five axes of a 5-axis CNC machine are the linear axes X, Y, Z, and two rotatable A, B, or B, C axes. This allows the machine to machine from multiple directions and angles of the workpiece.
5-axis CNC machines can machine complex surfaces and shapes in a single pass, saving time on tool changes and re-clamping.
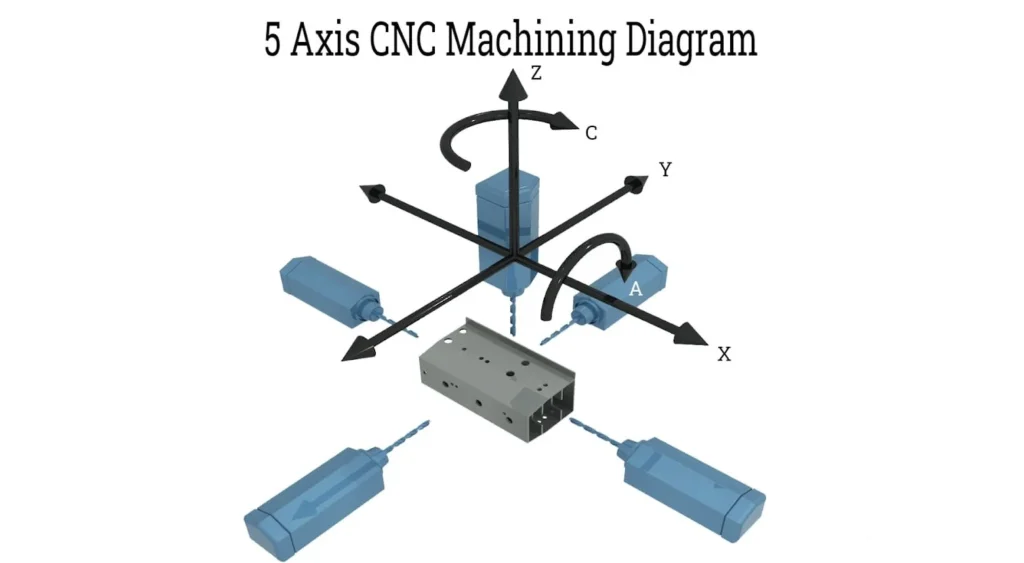
9-Axis CNC Machines
The 9-axis CNC machine can be said to be the cutting-edge equipment in the machining industry nowadays, which contains 3 linear axes X, Y, Z, and 6 rotary axes A, B, C, U, V, W. The 9-axis CNC machine can be said to be the cutting-edge equipment in the machining industry nowadays.
More axes means more machining freedom when machining workpieces, allowing more complex surfaces and shapes to be machined.
Advantages and limitations of CNC machining
Vantage
- High machining accuracy with minimal dimensional error.
- High degree of automation and less manual intervention can improve production efficiency.
- As long as the program remains the same, almost identical parts can be machined with consistent quality.
- Complex surfaces and shapes can be machined.
- Very suitable for mass production, can save a lot of labor costs
- There are many materials that can be processed.
Inferior
- High upfront cost investment, equipment, staff training, etc.
- Programming is difficult and requires specialized knowledge and experience, especially with complex parts.
- There is a limitation on the size of the workpiece and it is not possible to machine very large parts.
- Design changes are more cumbersome and require program changes.
- For small quantities and customized products, the cost advantage is not significant.
Application of numerical control technology
CNC technology can be said to be an advanced manufacturing technology, CNC’s full name is Computerized Numerical Control, through the computer control of the machine tool is almost no error, even if the error is far less than manual control. Therefore high precision, high efficiency, and high quality have become synonymous with CNC.
Almost many highly sophisticated industries are currently using CNC technology.
mechanical engineering
- Automobile manufacturing: engines, suspensions, frames, wheels, etc.
- Aerospace: Manufacture of aircraft components, rocket engine components, etc.
- Shipbuilding: Manufacture of hulls, propellers, etc.
- Railroad locomotive manufacturing: Manufacture of locomotive components.
Electronics industry.
- PCB Manufacturing: Manufacture of printed circuit boards.
- Electronic component processing: Manufacture of various electronic components.
Mold Manufacturing.
- Plastic Mold: Manufacture of plastic product molds.
- Die Casting Molds: Manufacture of metal casting molds.
Medical Device Manufacturing.
- Implants: Manufacture of medical devices such as artificial joints and bones.
- Medical instruments: Manufacture of surgical instruments, medical imaging equipment, etc.
Ask EVERGREEN for your next CNC machining project!
If you want to start a CNC machining program, no problem! But choosing the right machine for you will be a bit of a hassle, and you’ll need to train your staff to program, which can be a big upfront investment.
However there is another option, which is to outsource your CNC machining projects to manufacturers like Evergreen, if you outsource to Evergreen then you can have more time to develop new projects, and you can have complete peace of mind when handing over a project to Evergreen, we have a range of CNC machines available to meet all your needs.
Our team of engineers will also take care of your project, write to us to get a free quote.