What is Anodizing?
Anodizing Principle
You may sometimes feel confused, the same aluminum parts, some surfaces are easy to scratch, while some are very hard. ——This is actually the difference between aluminum pieces that are anodized and those that are not. When you put an aluminum part as a positive electrode into an electrolyte (usually dilute sulfuric acid) and electrify it, the surface of the aluminum part will gradually produce a protective layer of aluminum oxide. This artificially accelerated oxidation process is what we call anodizing.
If you look at this oxide film with an electron microscope, you’ll see that it’s not smooth and flat, but rather a structure covered with honeycomb-like micropores. These pores are the key to subsequent dyeing; they attract dye molecules, which is why your phone case can take on a variety of dazzling colour effects.
5 Core Advantages of Anodizing
Of course, we choose anodizing is never just for the face value, the following five practical values are the focus:
① Abrasion resistance is 3-5 times higher than ordinary aluminum parts (oxide film intact in key scratch test)
② Corrosion resistance doubled, salt spray test up to 500 hours
③ The oxide film generated by anodizing is a perfect insulating layer, withstanding a voltage of 500V when the film thickness is 20μm.
④ The pores on the surface can effectively and long-lastingly adhere to the colour, will not fall off, than the life of the spray paint for more than 5 years.
⑤ Enhances adhesion of glue, and the microporous structure provides mechanical anchoring.
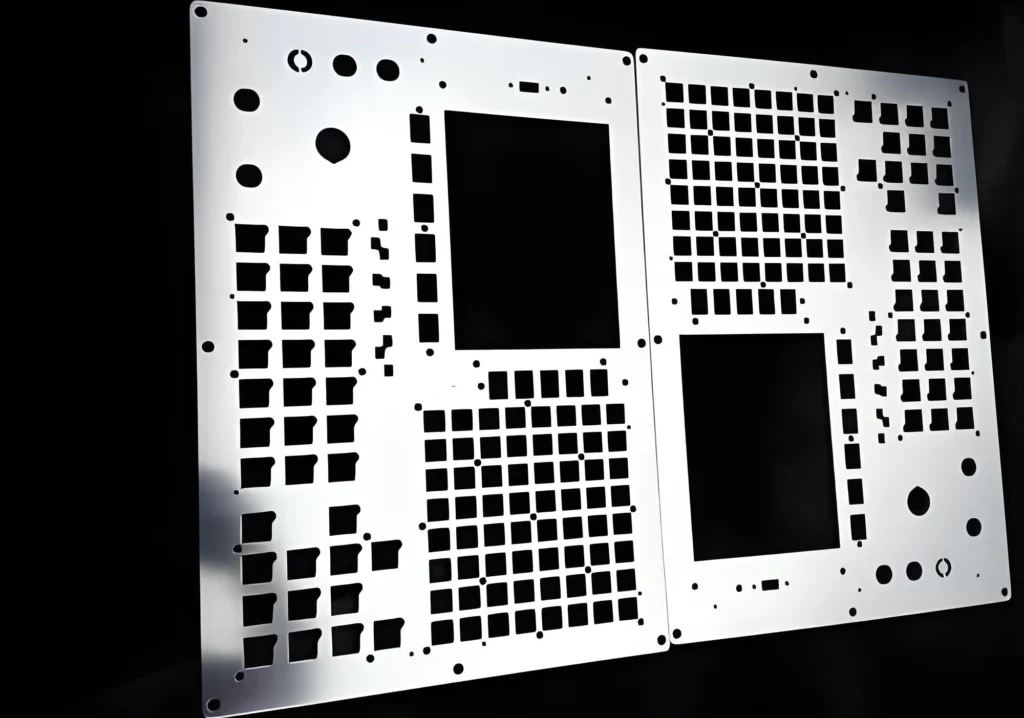
What Scenarios Necessitate The Use of Anodizing?
Anodizing processes must be considered when your parts face the following challenges:
- Some cabinets and enclosures that are exposed to the outdoors for a long period of time
- Parts that come into frequent contact with sweat or corrosive liquids
- Conductivity may occur, and hazardous scenarios may occur
- Precision instrument components requiring precise dimensional control
- Electronic housings and decorations with individual colour requirements
Preparation for Anodizing
Basic Tools
- Use of plastic drums as electrolysis cells (food-grade HDPE material, acid and alkali resistant)
- 12V/5A DC power supply (old computer power supply can be modified)
- Preferably with titanium hangers (to avoid contamination of the electrolyte)
- Thermometer (range 0-30°C, accuracy ±0.5°C)
- Electronic scales (accurate to 0.1 g, accuracy required for solution preparation)
Chemical Reagent
- Electrolyte can use battery-grade sulfuric acid (less impurities, more stable and more environmentally friendly)
- If there is a need for dyeing, it is recommended to use anodized special dyes (ordinary textile dyes will fade)
- Room temperature sealer, nickel fluoride, is more common on the market (60% less energy consumption than hot water sealing)
If you’re new to this, it’s recommended to start with a 500ml bottle, enough to handle 10 cell phone-sized parts.
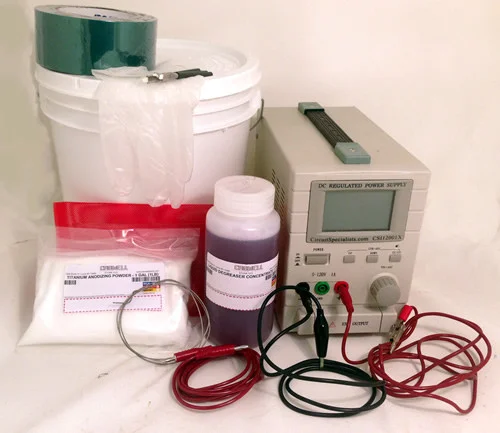
Protective Equipment
Anodizing involves a certain amount of risk, so be sure to wear protective equipment when handling:
- Fully closed goggles (risk of acid mist intrusion still on the sides of ordinary glasses)
- Butyl rubber gloves (kitchen latex gloves corrode in 10 seconds)
- Polyvinyl chloride aprons (cotton aprons will carbonize when exposed to acid)
Emergency Solution: Always keep a 5% baking soda solution next to the operating table.
Pre-Treatment of Aluminum Parts
Aluminum Alloy Material Identification
Whether it’s aluminum or aluminum alloy, magnets won’t pick it up. Common:
- 6061 aluminum alloy, suitable for hard oxidation, dark gray after treatment.
- 7075 Aviation Aluminum need to extend the oxidation time; if the time period, the film layer is brittle.
- Die-casting aluminum, with air holes on the surface, needs to be sandblasted before anodizing.
Deep Cleansing
- Hot water + detergent, the main purpose is to remove the surface of the oil, washed to touch the “squeaky” sound is considered clean.
- Soak in 10% NaOH solution for 3 minutes and wait until uniform bubbles appear and remove immediately.
- Neutralize with a 30% nitric acid solution until the surface has a uniform matte finish.
- Finally, rinse with deionized water; calcium ions in tap water can cause spots to
Surface Polishing
If you want a mirror effect, try the following two methods:
- Mechanical polishing: step by step with 800→3000 mesh sandpaper, and finally with wool wheel+drilling plaster
- Chemical polishing: phosphoric acid + nitric acid mixture, 70 ℃ immersion 45 seconds, this process will produce brown smoke, needs strong ventilation
It is recommended to test with an edge first, as the difference in polishing speed can be up to 200% for different alloys!
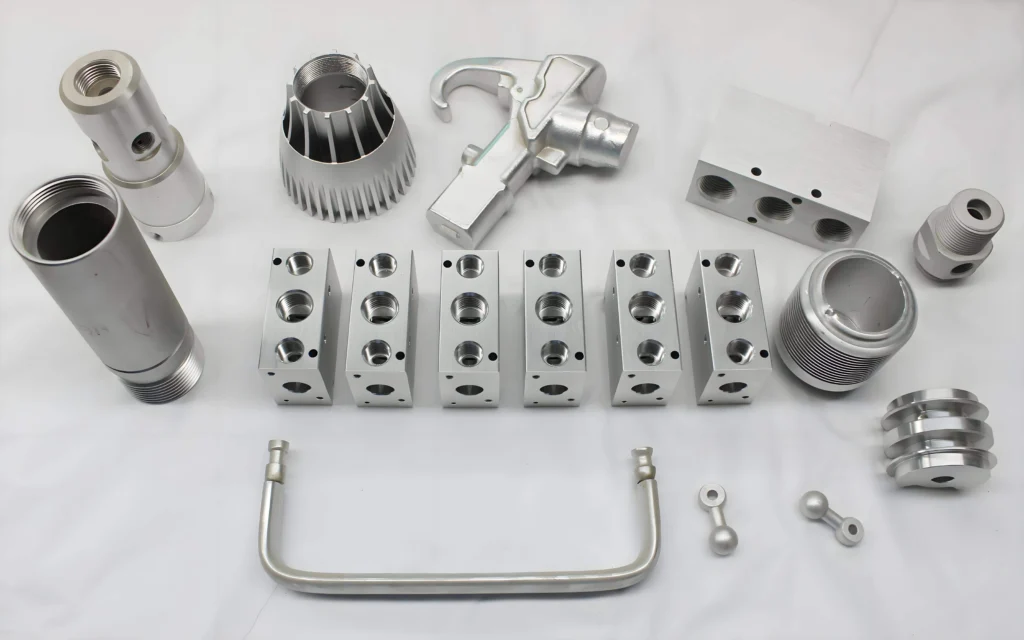
Anodizing Environment
Ventilation System
Teaches you to remodel your kitchen range hood for $200:
- Remove the original screen and add a PVC air guide pipe (15cm in diameter)
- Installation of an adjustable windshield 30cm above the operating table
- Addition of activated carbon filter layer (monthly replacement)
Measured to remove 95% of acid mist in less than a minute.
Electrolyte Temperature
The temperature of the electrolyte will have a direct effect on the quality of the oxide film:
- 18℃: optimal film forming temperature
- 22°C: The film starts to soften
- 25°C: possible risk of chalking
Chemical Storage
You can organize the chemicals in your studio according to the “three-zone segregation method”:
- Red zone: strong acids and alkalis (acid-resistant mats on the floor)
- Yellow zone: organic solvents (storage in explosion-proof cabinets)
- Green zone: prepared solution (clearly labelled with concentration/date of preparation)
The spill response kit shall contain: siphon, neutralizer, and sorbent cotton.
Anodizing Practice
Electrolyte Ratio
- The ratio of sulfuric acid: distilled water is 1:5 (v/v)
- Temperature control at 18±2°C
- Current density 1.2A/dm²
IMPORTANT: ALWAYS pour acid into water! Otherwise, it will splash violently.
Electronic Circuit Connection
Key Details:
- Preferably lead sheet for cathode (twice the area of the workpiece)
- Workpiece spacing >3cm (to prevent shielding effect)
- Use of collets (to avoid poor contact)
Voltage and Current
Keep this film thickness formula in mind:
Film thickness (μm) = 0.3 x current density (A/dm²) x time (min)
Example: want 15μm film layer → 0.3×1.2×42≈15μm
Real-Time Monitoring of The Oxidation Process
During the anodizing process, you need to monitor the situation in the electrolytic cell in real time to avoid unnecessary accidents.
Normal phenomenon:
- Produces uniform fine bubbles, no need to worry, this is the cathode to produce hydrogen gas
- Electrolysis for a period of time, the solution is slightly bluish, which is the dissolution of the aluminum ions.
Danger signals:
- Violent bubbling occurs during electrolysis → This indicates that the current is too high
- Aluminum parts are blackened after electrolysis → This indicates that the electrolyte is contaminated.
- Electrolyte cloudy → Temperature out of control
Staining & Sealing
Dye Selection
When you choose a colorant, make sure you pay attention to these two key parameters:
- pH range: most dyes develop best between 4.5-5.5 (can be tested with pH test paper)
- Lightfastness level: Selection of dyes ≥ 7 (ASTM D4303 standard)
Lesson: I once dyed a cell phone case made of aluminum with red textile dye that faded to pink in two weeks in the sun. Then I switched to a special metallic dye that still retains 90% color saturation after three years. Remember: treat up to 50g of aluminum per liter of dye solution or you’ll get discoloration!
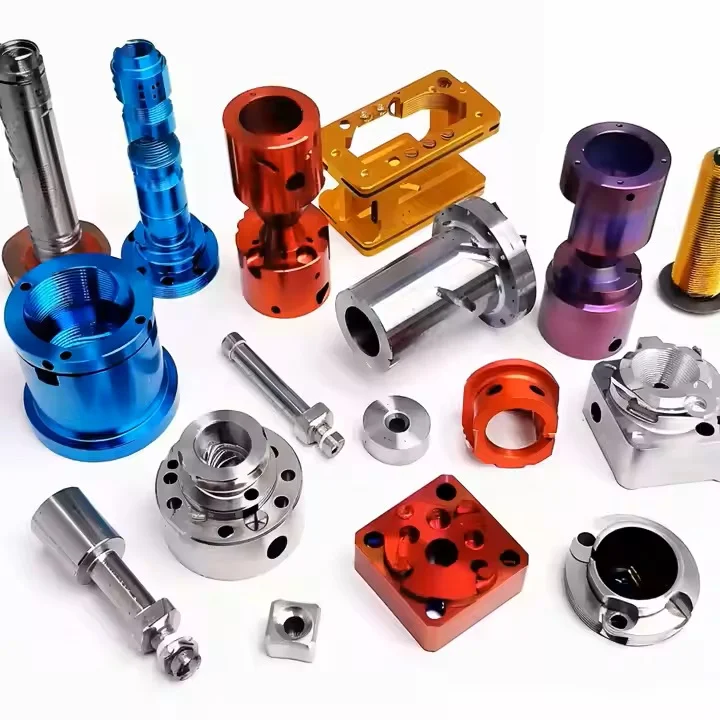
Gradient Colouring Tips
If you want to make a star gradient effect, follow this timeline:
- Pre-soak treatment: 2 minutes in warm water at 60°C (opens more micropores)
- The first stage of dyeing: immersed in the dye solution 1/3 depth, let stand for 8 minutes
- Second stain: move down to 2/3 depth of immersion and hold for 6 minutes
- Full immersion colouring: Completely submerge the workpiece for 4 minutes.
KEY POINT: When removing the part, immediately rinse the transition zone with deionized water!
Hole Sealing Treatment Program
Here are two treatment options for sealing holes that you can look at and compare:
Norm | Boiling water sealing | Nickel salt sealing |
(manufacturing, production, et.c) costs | 0.3 yuan per piece | 2.5 yuan per piece |
timing | 45 minutes | 15 minutes. |
corrosion resistance | Passed 48h salt spray test | Passed 96h salt spray test |
environmental | non-polluting | Nickel-containing wastewater requires special treatment |
Quality Inspection and Troubleshooting
Oxide Film Thickness
Inspection methods: Eddy current thickness gauge or metallographic microtome; these methods are highly accurate but require destruction of the aluminum part.
Standard range: Conventional decorative film 5-25μm, hard oxide film 25-100μm.
Film Hardness
If you have a hardness tester, you can use it to conduct the test, so that the data obtained will be more accurate (HV ≥ 300 for qualified hard oxidation).
If you don’t have professional equipment, you can use a coin or key to scratch the surface of the aluminum part, the hard oxide film should be free of scratches visible to the naked eye (load ≥ 5N).
Hole Sealing Quality
Acid Dye Absorption Test: If the sealing holes are of good quality, then there will be no dye residue on the surface of the aluminum parts.
Boiling water weight loss method: weight loss after sealing the hole ≤30mg/dm².
Exfoliation of The Oxide Film
Probable Cause:
- Pre-treatment is not clean, degreasing, and acid washing is not thorough, the surface residual grease or oxidized skin.
- The electrolyte temperature is too high, resulting in a loose film layer.
- It could also be unstable voltage/current density during electrolysis.
Solution:
- Enhance pre-treatment: add ultrasonic cleaning or extend pickling time.
- Control the electrolyte temperature at 18-22℃, if a hard oxide layer is required then the temperature is controlled at ≤10℃.
- Check rectifier output stability and adjust current density to 1.5-2.5A/dm².
Surface White Spots or Foggy Defects
Probable Cause:
- Incomplete water washing after oxidation and residual acid corroded the localized oxide layer.
- Abnormal sealing process parameters, insufficient temperature or time.
- Aluminum itself has segregation or inclusions.
Solution:
- Add multi-stage counter-current water washing to ensure that there is no residual acid on the surface of the aluminum parts.
- The temperature of the nickel salt sealing hole was controlled at 80-90°C for ≥15 minutes.
- Spectral analysis of the aluminum composition was used to avoid Si content >5%.
Insufficient Corrosion Resistance
Probable Cause:
- Excessive oxide film porosity may be due to high electrolyte temperature or high current density.
- Incomplete sealing of holes, excessive use of sealing fluid, leading to aging or insufficient temperature.
- Microcracks are present in the oxide film, which are caused by cracking due to stress from thermal and cold shocks.
Solution:
- You might try lowering the temperature of the electrolyte to 15°C and the current density to the lower limit.
- To replace the sealing solution, you need to monitor the concentration of nickel salts in real time and top up when ≤ 1g/L.
Insufficient Film Hardness
Probable Cause:
- Electrolyte temperature is too high, hard oxidation needs ≤10℃.
- Insufficient current density or too short oxidation time.
- Other elements in aluminum alloys interfere, such as copper and zinc alloys.
Solution:
- A forced cooling system is used to control the temperature of the electrolyte within 10°C.
- Increase current density to 3-4A/dm² for longer oxidation times.
- Select the appropriate aluminum alloy, 6061, 7075, etc., are recommended.
Professional reminder: For every 10μm increase in film thickness, the size of the part will increase by about 1.2μm; precision parts need to be calculated in advance to compensate for the amount!
Neutralization of Waste Liquids
Anodized aluminum parts produced by the waste liquid, if not treated directly discharged, the environment will cause no small breakthrough, you can look at these several ways of waste liquid treatment:
- When disposing of acid waste, you can add calcium carbonate powder to it to neutralize the pH of the acid to 7 before discharging it.
- If the wastewater is alkaline, it can be adjusted by adding food-grade citric acid.
- For heavy metal liquids, it is recommended to put aluminum foil to replace metal ions.
- Organic solvents can be risky to handle, and we recommend sending them to a professional facility in a sealed jar.
About EVERGREEN
ENERGREEN Machinery is a manufacturing plant that combines casting, machining, sheet metal welding and forging, our factory total area reaches 15000+㎡ . You can trust your project to EVERGREEN and we will provide you with professional manufacturing services for the whole process.
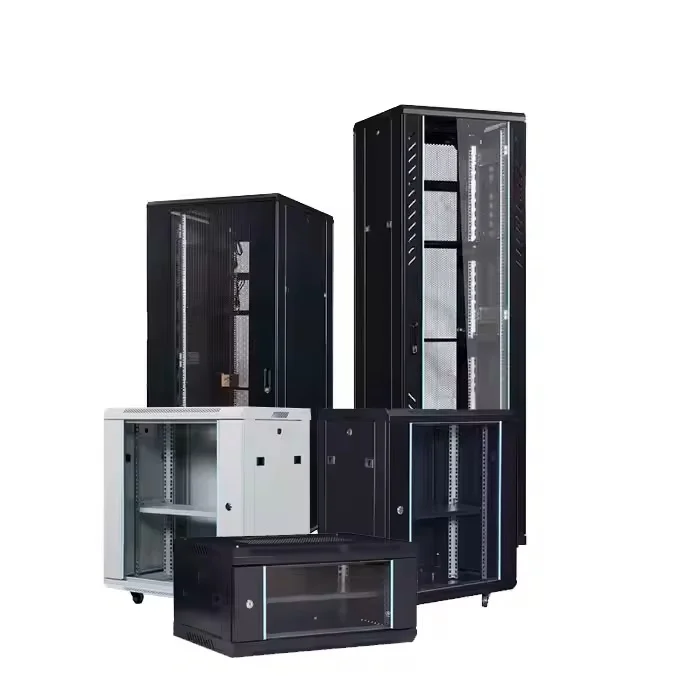
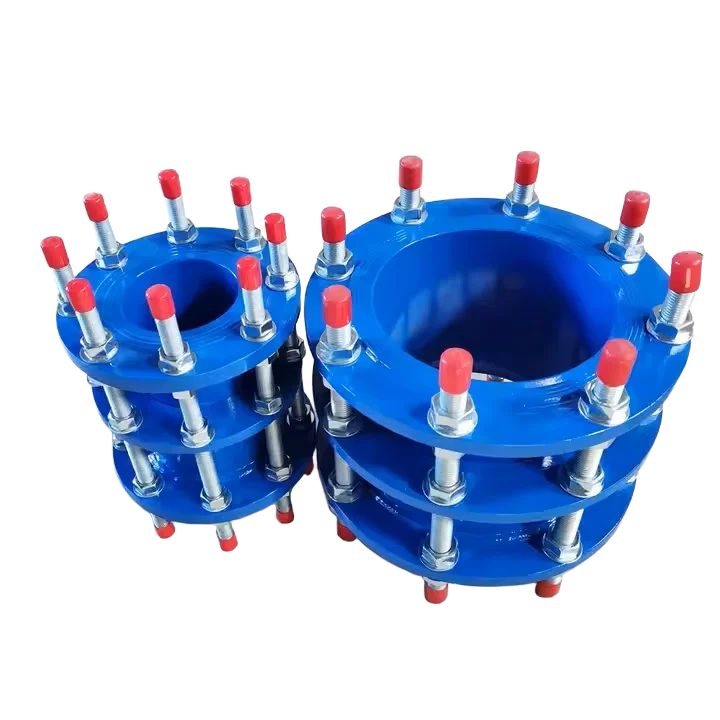
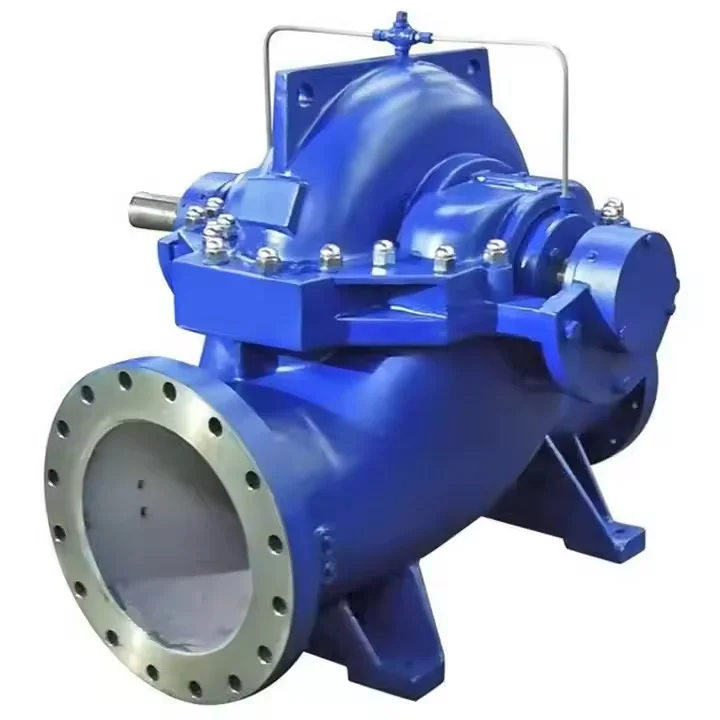
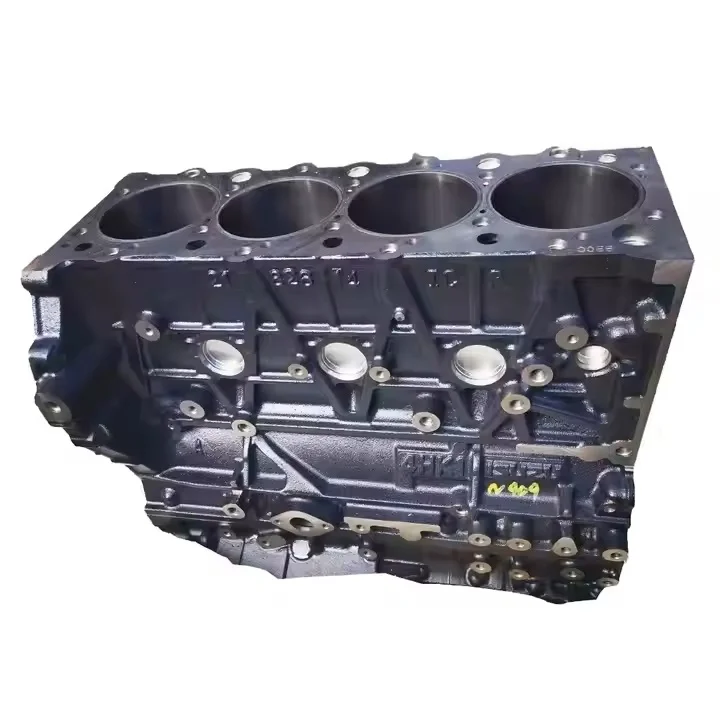